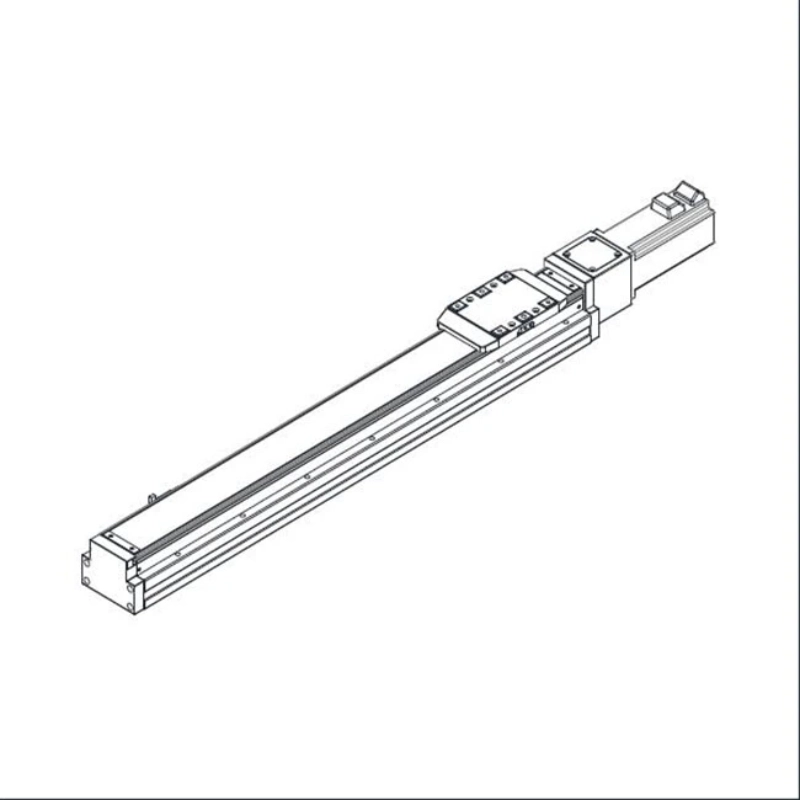
Screw Drive Linear Guideway
2023-05-12
57 Stepper Servo Motor
2023-05-1260 Closed-loop Servomotor
Although servo motors are designed to run at high speeds, they can accurately run at extremely low speeds under very precise control, even down to 1 rpm and below with proper preparation.
1. Product Introduction
Although servo motors are designed to run at high speeds, they can accurately run at extremely low speeds under very precise control, even down to 1 rpm and below with proper preparation. When properly utilized, steppers are accurate and are usually a more economical solution for low-speed applications (less than 1,000 rpm). However, above 1,000 rpm, a stepper motor’s torque begins to fall off, the result of magnetic circuit time constants and core losses.
In contrast, servo motors with comparable torque do not start to fall off until around 2,000 to 4,000 rpm or more (Figure B). Direct-drive servo applications powering high-inertia loads are typically found utilizing speeds < 1000 rpm, while typical servo applications with a mechanically advantaged drive train are likely to be found using any speed within its working envelope of capability.
With a required speed range between 1,000 to 3,000 rpm, the motor type that should be used may be determined by such application requirements as horsepower, peak torque at speed, continuous (RMS) torque and repeatability.
At stall (low speeds < 50 steps/second or 15 rpm) or when holding a load with no movement, stepper motors, especially with oversized rotors, can produce more torque than servos for a given frame size (although newer servo motor designs are encroaching on this). All that torque lets steppers produce extremely accurate and stiff low-speed motion without a gearbox or other mechanical advantage.
In contrast, Direct Drive servo motors with higher pole count and high-resolution feedback are often utilized for industrial process applications requiring typical velocities of less than 1000 rpm without a mechanical advantage such as a gearhead.
When a stepper motor is at rest, it uses continuous energy and there is absolutely no movement (unless overloaded), and when not powered its detent torque capability can be used to hold position.
In contrast, a servo motor is never at rest when ON, due to the constant closed loop error correction, while only using the energy required to maintain its commanded position. The constantly varying position-loop error causes the servo’s output shaft to move back-and-forth (though it should not be noticeable), while continuously looking for minimum error. This continuous back-and-forth actuator motion is called, hunting, similar to another term, dither, a purposely induced actuator movement (e.g. valve to continuously overcome the issues of stiction). The physical displacement during hunting, typically involves only a few feedback counts, relative to the total resolution: what is unnoticeable in most applications, can be unacceptable in others (higher resolution feedback devices reduce the typical hunting delta).
Where repeatability and resolution are an issue, traditionally servo motor territory, steppers may now be considered. For steppers, the requirement is that the load must be predictable, or subject to only small external forces and disturbances, where tight coordination between axes is not required. Steppers, running open loop, can save an initial machine cost of greater than 20-30% over comparable servo solutions.
2. Product parameters.
60CSM30 stepper servo motor
3. Product qualification:
4. Deliver, shipping and serving:
5. FAQ:
Accuracy and Resolution
Stepper systems have a difference between their theoretical and actual resolution. For example, a two-phase, full stepping, 1.8° step-angle motor may have 200 possible positions in one revolution (360°/1.8°), but whether or not it’s achieved depends on how the motor was sized for the application. The same is true of half stepping and microstepping motor drive modes. A 1.8° microstepper, though specified as having ten microsteps per each full step, cannot necessarily find any position within 0.18°.
Additionally, several commanded microsteps may be required before there is enough torque build-up to overcome friction and load inertia. In a real-world situation, the motor could easily jump one or more microsteps beyond the number commanded and stabilize there. When positioning-resolution requirements need to exceed 200 steps per revolution, steppers may utilize a feedback encoder to achieve upwards of 1000 steps/rev. Five-phase motors and microstepping motors (with caution) can also improve on the steps/rev.
Servo motor resolution is theoretically infinite, but in closed-loop operation, system positioning depends primarily on the resolution of the feedback device be it a sine encoder, resolver or a digital (TTL) type encoder. Today’s high resolution feedback devices can approach between 221 [2,097,152] to 228 [268,435,456], counts per motor revolution, plus the optional multi-turn capability (typically up to 4096 turns). Multi-turn capable feedback devices are available for an axis’ absolute position on machine power-up eliminating the initial axis power-up homing cycle.
Repeatability
Servo motors are extremely repeatable because they run closed loop. But steppers can be just as repeatable in many applications, especially when running in one direction. However, when an Idle Current Reduction (ICR) mode is utilized and/or the load increases (e.g. as during direction reversal) and exceeds the capability of the stepper the situation changes. Similar to how a gearbox must take up backlash, the stepper must catch up to system command. During the first move in a new direction, motor accuracy is affected, because the stepper is overcoming inertia and friction (effects of the load). Once that happens, the system regains its specified repeatability, but it may have lost or gained actual position steps over those commanded.
Input Power
A step motor is equivalent to an inductor in series with a resistance and as a result, the current that produces torque requires time to rise. This time, limits the speed for a given voltage, so increasing the motor’s speed in a given application, may require higher voltages.
A servo system works similarly, but working within its capability envelope, the drive’s control loops will present the required voltage and current to the servo motor to meet the demand of the load relative to its command and feedback error. In contrast, when a servo motor system is forced to work (for whatever reason) outside its operational envelope, even for a millisecond, it is no longer under control and thus, not operating as a servo.
Conclusion
Both technologies are a clear choice in today’s mechatronic machine designs. However, once the advantages and disadvantages of servo and stepper motor systems are clearly understood, especially relative to the process or work to be performed, the best selection for a given application becomes much clearer.
Assuming the desired process can be accomplished with either a stepper or servo motor solution, with the repeatability, accuracy and flexibility requirements, for present and future needs, the remaining considerations would likely be environment, life expectancy, operating noise, and/or energy utilization.
When specific requirements allow for either technology, one should utilize discernment and foresight, with the specific knowledge of the considered working process or job to be performed, possible future needs, and the designer’s machine experience.
IP65-rated step motors for wet, dusty industrial factory environments
Applied Motion Products offers an extended line of stepper motors with IP65 ratings that are dustproof and resistant to water pressure impact, making them suitable for use in wet and dusty applications.
Using advanced seal protection technology, the IP65-rated step motors feature sealed laminations, an oil shaft seal, internal corrosion-resistant film coating, gaskets for mechanical joints and an integral 10-ft. shielded cable that offers protection against the ingress of dust and resistance to low-pressure water jets. For improved protection in high-humidity environments, an advanced coating is available as an option.