
60 Closed-loop Servomotor
2023-05-12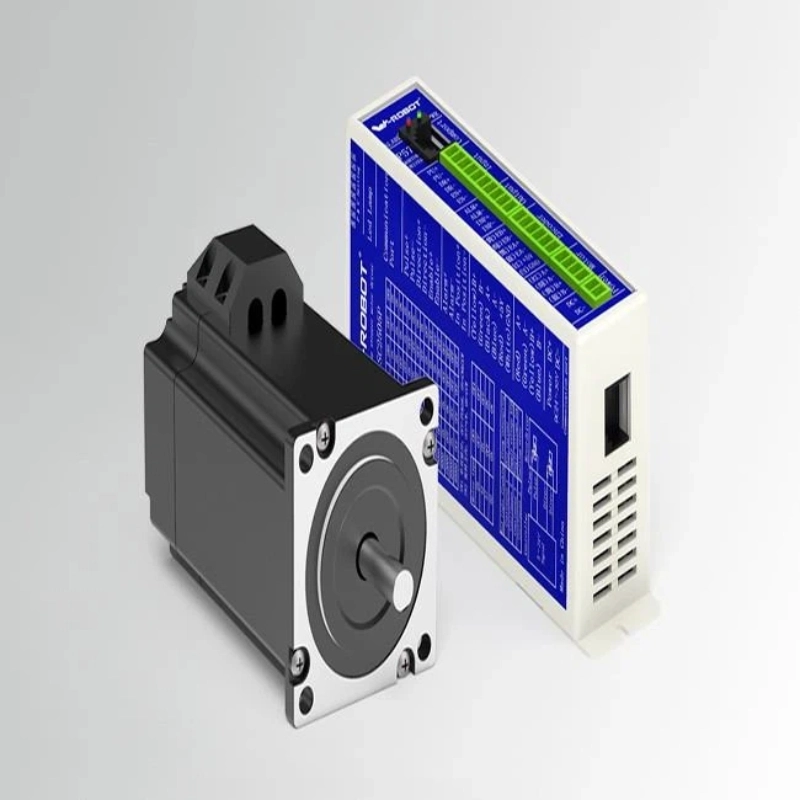
42 Stepping Servo Motor
2023-05-1257 Stepper Servo Motor
Each technology has its niche, and since the selection of either of these technologies for a given application affects its chance of success
1. Product Introduction
Stepper Motor or Servo Motor; Which Should it be?
Each technology has its niche, and since the selection of either of these technologies for a given application affects its chance of success, it is important for the machine designer to select the best motor-drive system for the application, while considering the technical advantages and disadvantages of both.
It is all about utilizing these technologies with balance to achieve the desired process performance for a given machine design while balancing cost versus the capability of the required mechanism.
Machine designers shouldn’t limit utilization of steppers or servos by a predetermined mindset or comfort level, but learn where each technology works best for controlling a specific mechanism and process to be performed.
2. Product parameters.
57CSM stepper servo motor
3. Product qualification:
4. Deliver, shipping and serving:
5. FAQ:
Stepper Motor System Overview
Stepper motors have several major advantages over servo systems. They are typically lower cost, have common NEMA mountings, offer lower torque options, require less costly cabling, and their open loop motion control component makes machine integration simplistic and provides ease-of-use to end users.
Torque and Speed Considerations
The issue of whether to use a stepper or servo is dictated by the application in most cases. Steppers are typically sized for twice their continuous requirements for additional acceleration and/or deceleration torque capability or for a required peak torque.
In contrast, servo motors are generally sized for the specific application velocities and torques for maximum intermittent acceleration/deceleration, holding torque (if applicable), and continuous RMS requirements over the complete motion profile.
In general, if an application requires high-throughput, high-speed, and high-bandwidth capability for disturbance correction, and/or high-rpm, with or without tight coordination between axes, servo motors are the best option. If point-to-point position performance and rpm requirements are modest, (as a function of the process loads and expected disturbances) steppers may be a better choice. Additionally, when the loads are within reason, a stepper’s ability to hold position (using holding torque with power and detent torque without power) can be an advantage.
Speed-torque curves highlight the difference between stepper and AC permanent magnet (PM) servo motors of equal volume. Steppers typically generate higher continuous torque at lower speeds than servo motors. However, servo motors produce intermittent peak torques in this same low-speed range and produce peak and continuous torques over a much wider-higher speed range.
Automated machine axes for adjustment and setup as well as video axes for inspection, are applications that stepper systems fulfill well. Steppers are especially ideal for these type axes because they tend to be easier to design into control systems and less expensive on initial setup. When an axis for a given setup can be locked into place they are less expensive to operate (e.g. optional ON/OFF reduced power mode). Additionally, when properly applied, steppers are less prone to failure because of their simplistic open-loop control, which only requires winding-to-drive match-up versus motor-drive-to-mechanism tuning required with feedback circuits of a closed-loop system.
Stepper Drives
Newer design techniques have improved step motor performance by the utilization of: built-in feedback, end-of-move damping (for reduced settling times while maximizing accuracy), soft-start (to reduce jerk on power-up), anti-resonance modes (for optimizing torque, stability, and noise reduction – audible or otherwise), Idle Current Reduction (IRC – for reduced motor heating during standstill) and easily controlled operation modes between full-step, half-step and microstepping.
Although most properly sized steppers are extremely accurate running open loop in the selected step mode, built-in feedback provides additional precision without the cost of an external feedback device. Microstepping techniques result in smoother torque and motion at low speeds and greater resolution at high speeds with the reduction of step size from full-step/half-step.
Modern Stepper Developments
Modern steppers are available in larger power ratings than earlier generation steppers. Newer design techniques have led to smaller airgaps, stronger magnets, physically larger magnets and rotor oversizing. Increasing the rotor’s diameter generates more torque per unit volume. For this technique, the physical frame size and winding of the step motor stays the same while the rotor’s diameter and inertia are increased. Of course, the larger rotor inertia can affect acceleration and deceleration times for a given application; but this method opens up more applications to a given stepper frame size by the effective decreased ratio of the load (J_load) to motor rotor (Jm) inertia. Generally, step motor systems are sized with a J_load : Jm of less than 30:1, but with slower accelerations and decelerations and advanced microstepping operation, inertia ratios of 200:1 are achievable.
With Stall Detection now being handled electronically within today’s modern stepper drives, optional feedback devices are typically utilized for position correction due to component misalignment, noise, and/or lost pulse (position) information. A step motor with feedback, depending on the stepper drive, will have less velocity ripple and use less power than open-loop equivalents and will have higher residual torque at low speeds than an equivalent three-phase servo motor. Thus, the designer must use discernment in regard to the work to be performed because step motor applications requiring feedback can approach the cost of a servo system and what may be an operational advantage in one application may be a disadvantage in another. Closed-loop stepper systems do not technically compete well against the lower priced servo motor system; so the pros and cons of both type systems should be carefully considered for the application.
Servo Motor System Overview
Servo motors have several distinct advantages over steppers. They can generate high torque over a wide speed range on demand, and are available in wider torque ranges and higher voltages (up to 480 Vac). They respond to disturbances with a torque much greater than their continuous capability and use only the power required to accomplish the commanded motion and are compact.
Servo Drives
Motor-drive compensation often referred to as tuning or comp, once considered the bane process of servo users is, for the most part, history. Today, the newest digital servo drive technologies have enhanced software and hardware capabilities for improved user experience and offer remarkable compensation flexibility. In fact, some servo systems automatically configure the motor, drive and feedback, and tune themselves as well. Servo drives that tune themselves automatically adapt to the given motor-drive-mechanism, without a decrease in performance and with little need for further fine tuning of the control loops.
Hot Tags: screw drive linear guideway, China, manufacturers, suppliers, factory, wholesale, buy, customized, bulk, in stock, Semi-closed Belt Drive Linear Actuator, Fully-closed Screw Drive Linear Actuator, Robot, XY Linear Motor, Linear Guideway Motion Systems, Dust-free Environment Belt Drive Linear Actuator